What are the Mainstream Capacitor Application Production Processes?
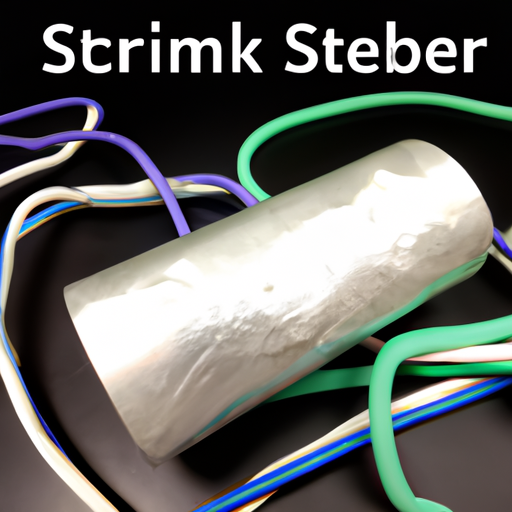
I. Introduction
Capacitors are fundamental components in electronic devices, serving as energy storage elements that play a crucial role in various applications, from power supply circuits to signal processing. They store electrical energy temporarily and release it when needed, making them essential for maintaining voltage levels, filtering signals, and stabilizing power supplies. As technology advances, the demand for capacitors continues to grow, leading to the development of various types and production processes tailored to meet specific needs. This blog post will explore the mainstream capacitor application production processes, providing insights into the types of capacitors, raw materials, production methods, quality control, challenges, and future trends.
II. Types of Capacitors
Capacitors come in various types, each with unique characteristics and applications:
A. Ceramic Capacitors
Ceramic capacitors are widely used due to their small size, reliability, and cost-effectiveness. They are made from ceramic materials that serve as the dielectric. Common applications include decoupling, filtering, and timing circuits.
B. Electrolytic Capacitors
Electrolytic capacitors are polarized components that offer high capacitance values in a compact form. They are commonly used in power supply circuits, audio equipment, and energy storage applications. Their construction involves an electrolyte that enhances capacitance.
C. Film Capacitors
Film capacitors utilize thin plastic films as dielectrics, providing excellent stability and low losses. They are often used in applications requiring high precision, such as audio equipment, power electronics, and signal processing.
D. Tantalum Capacitors
Tantalum capacitors are known for their high capacitance-to-volume ratio and reliability. They are often used in applications where space is limited, such as in mobile devices and aerospace electronics.
E. Supercapacitors
Supercapacitors, or ultracapacitors, are energy storage devices that bridge the gap between traditional capacitors and batteries. They offer high energy density and rapid charge/discharge capabilities, making them suitable for applications like regenerative braking and energy harvesting.
III. Raw Materials for Capacitor Production
The production of capacitors requires various raw materials, each contributing to the performance and reliability of the final product.
A. Dielectric Materials
Dielectric materials are crucial for capacitor function, as they determine the capacitor's capacitance and voltage rating. Common dielectric materials include ceramic, polyester, polypropylene, and tantalum oxide, each with distinct properties that suit different applications.
B. Conductive Materials
Conductive materials, such as aluminum, tantalum, and silver, are used for the electrodes in capacitors. The choice of conductive material affects the capacitor's performance, including its equivalent series resistance (ESR) and overall efficiency.
C. Packaging Materials
Packaging materials protect capacitors from environmental factors and mechanical stress. Common packaging materials include plastic, aluminum, and epoxy resins, which provide insulation and structural integrity.
IV. Production Processes
The production processes for capacitors vary depending on the type. Here, we will explore the mainstream production methods for different capacitor types.
A. Ceramic Capacitor Production
1. **Material Preparation**: The production begins with the preparation of ceramic powders, which are mixed with additives to achieve desired properties.
2. **Dielectric Layer Formation**: The mixture is then pressed into thin layers, which are subsequently dried to remove moisture.
3. **Electrode Application**: Conductive materials are applied to the dielectric layers, forming electrodes.
4. **Sintering Process**: The assembled layers are subjected to high temperatures in a sintering furnace, which densifies the ceramic and enhances its dielectric properties.
5. **Finishing and Testing**: After cooling, the capacitors are cut, finished, and tested for quality assurance.
B. Electrolytic Capacitor Production
1. **Anode Foil Preparation**: The process starts with the preparation of aluminum or tantalum foils, which are etched to increase surface area.
2. **Dielectric Formation**: A thin oxide layer is formed on the anode foil through an electrochemical process, serving as the dielectric.
3. **Electrolyte Filling**: The capacitor is filled with an electrolyte solution, which enhances capacitance.
4. **Sealing and Packaging**: The capacitor is sealed to prevent leakage and packaged for distribution.
C. Film Capacitor Production
1. **Film Extrusion**: Plastic films are extruded to the desired thickness and width.
2. **Metallization**: A thin layer of metal is deposited onto the film to create electrodes.
3. **Winding and Cutting**: The metallized film is wound into a cylindrical shape and cut to size.
4. **Encapsulation and Testing**: The capacitors are encapsulated in protective materials and subjected to rigorous testing.
D. Tantalum Capacitor Production
1. **Tantalum Powder Preparation**: Tantalum powder is processed to achieve the desired particle size and purity.
2. **Anode Formation**: The powder is compacted and sintered to form the anode.
3. **Dielectric Formation**: An oxide layer is formed on the anode through an electrochemical process.
4. **Cathode Application**: A conductive layer is applied to the dielectric, completing the capacitor structure.
5. **Packaging and Testing**: The capacitors are packaged and tested for performance and reliability.
E. Supercapacitor Production
1. **Electrode Preparation**: Carbon-based materials are processed to create high-surface-area electrodes.
2. **Electrolyte Selection**: An appropriate electrolyte is chosen based on the desired performance characteristics.
3. **Assembly and Packaging**: The electrodes and electrolyte are assembled into a cell, which is then packaged for use.
V. Quality Control and Testing
Quality control is paramount in capacitor production to ensure reliability and performance. Various testing methods are employed, including:
A. Importance of Quality Control
Quality control helps identify defects and ensures that capacitors meet industry standards and specifications. It is essential for maintaining customer trust and product reliability.
B. Testing Methods for Different Types of Capacitors
1. **Electrical Testing**: Capacitors are tested for capacitance, ESR, and leakage current to ensure they meet performance specifications.
2. **Environmental Testing**: Capacitors undergo tests to assess their performance under different environmental conditions, such as temperature and humidity.
3. **Reliability Testing**: Long-term reliability tests are conducted to evaluate the lifespan and durability of capacitors under stress conditions.
VI. Challenges in Capacitor Production
The capacitor production industry faces several challenges, including:
A. Material Sourcing and Sustainability
Sourcing raw materials, especially rare materials like tantalum, poses challenges related to sustainability and ethical sourcing practices.
B. Technological Advancements and Innovation
Rapid technological advancements require manufacturers to continuously innovate and adapt their production processes to meet changing market demands.
C. Market Demand and Competition
The growing demand for capacitors in various industries leads to increased competition, necessitating efficient production methods and cost management.
VII. Future Trends in Capacitor Production
The future of capacitor production is shaped by several emerging trends:
A. Emerging Technologies
Advancements in materials science and manufacturing technologies are expected to enhance capacitor performance and reduce production costs.
B. Eco-Friendly Materials and Processes
There is a growing emphasis on using eco-friendly materials and sustainable production processes to minimize environmental impact.
C. Miniaturization and Performance Enhancement
As electronic devices become smaller and more powerful, the demand for miniaturized capacitors with enhanced performance characteristics will continue to rise.
VIII. Conclusion
Capacitors are integral components in modern electronic devices, and understanding their production processes is essential for appreciating their role in technology. From ceramic to supercapacitors, each type has unique characteristics and applications that cater to various needs. The production processes, while complex, ensure that capacitors meet the high standards required for reliability and performance. As the industry faces challenges and embraces future trends, the evolution of capacitor technology will undoubtedly play a significant role in advancing electronic innovation. The future of capacitor production looks promising, with opportunities for sustainability, efficiency, and enhanced performance on the horizon.
What are the Mainstream Capacitor Application Production Processes?
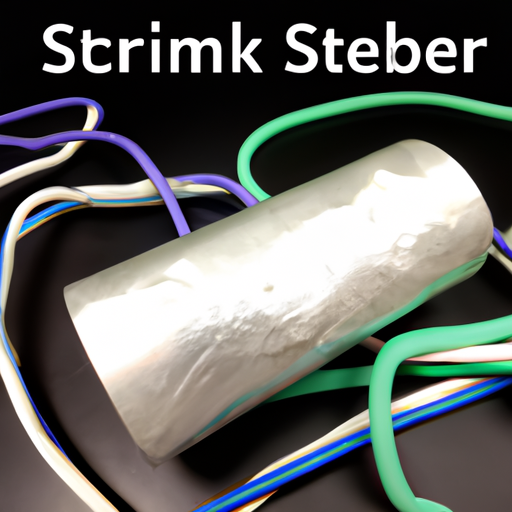
I. Introduction
Capacitors are fundamental components in electronic devices, serving as energy storage elements that play a crucial role in various applications, from power supply circuits to signal processing. They store electrical energy temporarily and release it when needed, making them essential for maintaining voltage levels, filtering signals, and stabilizing power supplies. As technology advances, the demand for capacitors continues to grow, leading to the development of various types and production processes tailored to meet specific needs. This blog post will explore the mainstream capacitor application production processes, providing insights into the types of capacitors, raw materials, production methods, quality control, challenges, and future trends.
II. Types of Capacitors
Capacitors come in various types, each with unique characteristics and applications:
A. Ceramic Capacitors
Ceramic capacitors are widely used due to their small size, reliability, and cost-effectiveness. They are made from ceramic materials that serve as the dielectric. Common applications include decoupling, filtering, and timing circuits.
B. Electrolytic Capacitors
Electrolytic capacitors are polarized components that offer high capacitance values in a compact form. They are commonly used in power supply circuits, audio equipment, and energy storage applications. Their construction involves an electrolyte that enhances capacitance.
C. Film Capacitors
Film capacitors utilize thin plastic films as dielectrics, providing excellent stability and low losses. They are often used in applications requiring high precision, such as audio equipment, power electronics, and signal processing.
D. Tantalum Capacitors
Tantalum capacitors are known for their high capacitance-to-volume ratio and reliability. They are often used in applications where space is limited, such as in mobile devices and aerospace electronics.
E. Supercapacitors
Supercapacitors, or ultracapacitors, are energy storage devices that bridge the gap between traditional capacitors and batteries. They offer high energy density and rapid charge/discharge capabilities, making them suitable for applications like regenerative braking and energy harvesting.
III. Raw Materials for Capacitor Production
The production of capacitors requires various raw materials, each contributing to the performance and reliability of the final product.
A. Dielectric Materials
Dielectric materials are crucial for capacitor function, as they determine the capacitor's capacitance and voltage rating. Common dielectric materials include ceramic, polyester, polypropylene, and tantalum oxide, each with distinct properties that suit different applications.
B. Conductive Materials
Conductive materials, such as aluminum, tantalum, and silver, are used for the electrodes in capacitors. The choice of conductive material affects the capacitor's performance, including its equivalent series resistance (ESR) and overall efficiency.
C. Packaging Materials
Packaging materials protect capacitors from environmental factors and mechanical stress. Common packaging materials include plastic, aluminum, and epoxy resins, which provide insulation and structural integrity.
IV. Production Processes
The production processes for capacitors vary depending on the type. Here, we will explore the mainstream production methods for different capacitor types.
A. Ceramic Capacitor Production
1. **Material Preparation**: The production begins with the preparation of ceramic powders, which are mixed with additives to achieve desired properties.
2. **Dielectric Layer Formation**: The mixture is then pressed into thin layers, which are subsequently dried to remove moisture.
3. **Electrode Application**: Conductive materials are applied to the dielectric layers, forming electrodes.
4. **Sintering Process**: The assembled layers are subjected to high temperatures in a sintering furnace, which densifies the ceramic and enhances its dielectric properties.
5. **Finishing and Testing**: After cooling, the capacitors are cut, finished, and tested for quality assurance.
B. Electrolytic Capacitor Production
1. **Anode Foil Preparation**: The process starts with the preparation of aluminum or tantalum foils, which are etched to increase surface area.
2. **Dielectric Formation**: A thin oxide layer is formed on the anode foil through an electrochemical process, serving as the dielectric.
3. **Electrolyte Filling**: The capacitor is filled with an electrolyte solution, which enhances capacitance.
4. **Sealing and Packaging**: The capacitor is sealed to prevent leakage and packaged for distribution.
C. Film Capacitor Production
1. **Film Extrusion**: Plastic films are extruded to the desired thickness and width.
2. **Metallization**: A thin layer of metal is deposited onto the film to create electrodes.
3. **Winding and Cutting**: The metallized film is wound into a cylindrical shape and cut to size.
4. **Encapsulation and Testing**: The capacitors are encapsulated in protective materials and subjected to rigorous testing.
D. Tantalum Capacitor Production
1. **Tantalum Powder Preparation**: Tantalum powder is processed to achieve the desired particle size and purity.
2. **Anode Formation**: The powder is compacted and sintered to form the anode.
3. **Dielectric Formation**: An oxide layer is formed on the anode through an electrochemical process.
4. **Cathode Application**: A conductive layer is applied to the dielectric, completing the capacitor structure.
5. **Packaging and Testing**: The capacitors are packaged and tested for performance and reliability.
E. Supercapacitor Production
1. **Electrode Preparation**: Carbon-based materials are processed to create high-surface-area electrodes.
2. **Electrolyte Selection**: An appropriate electrolyte is chosen based on the desired performance characteristics.
3. **Assembly and Packaging**: The electrodes and electrolyte are assembled into a cell, which is then packaged for use.
V. Quality Control and Testing
Quality control is paramount in capacitor production to ensure reliability and performance. Various testing methods are employed, including:
A. Importance of Quality Control
Quality control helps identify defects and ensures that capacitors meet industry standards and specifications. It is essential for maintaining customer trust and product reliability.
B. Testing Methods for Different Types of Capacitors
1. **Electrical Testing**: Capacitors are tested for capacitance, ESR, and leakage current to ensure they meet performance specifications.
2. **Environmental Testing**: Capacitors undergo tests to assess their performance under different environmental conditions, such as temperature and humidity.
3. **Reliability Testing**: Long-term reliability tests are conducted to evaluate the lifespan and durability of capacitors under stress conditions.
VI. Challenges in Capacitor Production
The capacitor production industry faces several challenges, including:
A. Material Sourcing and Sustainability
Sourcing raw materials, especially rare materials like tantalum, poses challenges related to sustainability and ethical sourcing practices.
B. Technological Advancements and Innovation
Rapid technological advancements require manufacturers to continuously innovate and adapt their production processes to meet changing market demands.
C. Market Demand and Competition
The growing demand for capacitors in various industries leads to increased competition, necessitating efficient production methods and cost management.
VII. Future Trends in Capacitor Production
The future of capacitor production is shaped by several emerging trends:
A. Emerging Technologies
Advancements in materials science and manufacturing technologies are expected to enhance capacitor performance and reduce production costs.
B. Eco-Friendly Materials and Processes
There is a growing emphasis on using eco-friendly materials and sustainable production processes to minimize environmental impact.
C. Miniaturization and Performance Enhancement
As electronic devices become smaller and more powerful, the demand for miniaturized capacitors with enhanced performance characteristics will continue to rise.
VIII. Conclusion
Capacitors are integral components in modern electronic devices, and understanding their production processes is essential for appreciating their role in technology. From ceramic to supercapacitors, each type has unique characteristics and applications that cater to various needs. The production processes, while complex, ensure that capacitors meet the high standards required for reliability and performance. As the industry faces challenges and embraces future trends, the evolution of capacitor technology will undoubtedly play a significant role in advancing electronic innovation. The future of capacitor production looks promising, with opportunities for sustainability, efficiency, and enhanced performance on the horizon.