What are the Latest Manufacturing Processes for Capacitor Casings?
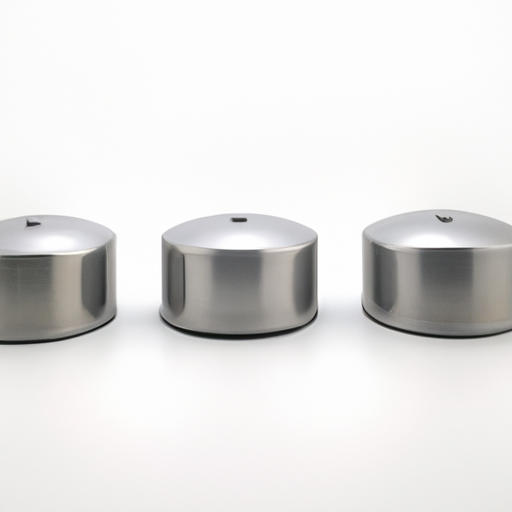
I. Introduction
Capacitors are essential components in electronic devices, serving as energy storage units that help regulate voltage and power flow. Their reliability and performance are critical to the overall functionality of electronic systems, from smartphones to industrial machinery. One of the key factors influencing a capacitor's performance is its casing, which protects the internal components and ensures durability under various operating conditions. This article explores the latest manufacturing processes for capacitor casings, highlighting innovations that enhance performance, sustainability, and efficiency.
II. Types of Capacitor Casings
Capacitor casings are made from various materials, each offering unique properties that affect the capacitor's performance.
A. Overview of Common Materials Used for Capacitor Casings
1. **Aluminum**: Aluminum casings are widely used due to their lightweight, corrosion resistance, and excellent thermal conductivity. They are particularly common in electrolytic capacitors.
2. **Plastic**: Plastic casings are favored for their versatility and cost-effectiveness. They can be molded into complex shapes, making them suitable for various capacitor designs.
3. **Ceramic**: Ceramic casings are known for their high dielectric strength and stability, making them ideal for high-frequency applications. They are often used in capacitors that require high reliability.
4. **Metalized Films**: These casings are made by depositing a thin layer of metal onto a dielectric film. They are lightweight and can be produced in various shapes, making them suitable for applications where space is limited.
B. Importance of Material Selection in Manufacturing Processes
The choice of material significantly impacts the manufacturing process, cost, and performance of the capacitor. For instance, aluminum casings may require stamping and forming techniques, while plastic casings can be produced using injection molding. Understanding the properties of each material helps manufacturers select the most appropriate processes for their specific applications.
III. Traditional Manufacturing Processes
A. Overview of Conventional Methods
1. **Stamping and Forming for Metal Casings**: Traditional methods for producing aluminum casings involve stamping sheets of metal into desired shapes. This process is efficient for high-volume production but can lead to material waste and limitations in design flexibility.
2. **Injection Molding for Plastic Casings**: Injection molding is a widely used technique for creating plastic casings. It allows for complex designs and high production rates but can be limited by the types of plastics that can be used and the initial setup costs.
B. Limitations of Traditional Processes
While traditional manufacturing methods have served the industry well, they come with several limitations:
1. **Material Waste**: Stamping processes often result in significant scrap material, leading to increased costs and environmental impact.
2. **Production Speed**: Although traditional methods can be efficient, they may not keep pace with the growing demand for rapid prototyping and customization.
3. **Design Flexibility**: Conventional methods can restrict design innovation, making it challenging to create unique or complex casing shapes.
IV. Latest Innovations in Manufacturing Processes
The capacitor casing manufacturing landscape is evolving, with several innovative processes emerging to address the limitations of traditional methods.
A. Advanced Materials
1. **Use of Nanomaterials for Enhanced Performance**: The incorporation of nanomaterials into capacitor casings can significantly enhance their performance. These materials can improve thermal conductivity, reduce weight, and increase the overall lifespan of capacitors.
2. **Biodegradable Materials for Environmentally Friendly Options**: As sustainability becomes a priority, manufacturers are exploring biodegradable materials for capacitor casings. These materials can reduce environmental impact and align with global efforts to minimize plastic waste.
B. Additive Manufacturing (3D Printing)
1. **Benefits of 3D Printing in Capacitor Casing Production**: Additive manufacturing, or 3D printing, allows for the creation of complex geometries that are difficult to achieve with traditional methods. This technology enables rapid prototyping, customization, and reduced material waste.
2. **Case Studies of Successful Implementations**: Companies like Panasonic and Vishay have successfully implemented 3D printing in their capacitor casing production, resulting in faster turnaround times and innovative designs that enhance performance.
C. Automation and Robotics
1. **Role of Automation in Improving Efficiency and Precision**: Automation technologies are revolutionizing capacitor casing manufacturing by increasing production speed and precision. Automated systems can handle repetitive tasks, reducing human error and improving overall quality.
2. **Examples of Robotic Applications in Casing Assembly**: Robotics are being used in various stages of the manufacturing process, from assembly to quality control. For instance, robotic arms can efficiently assemble capacitor components, ensuring consistent quality and reducing labor costs.
D. Hybrid Manufacturing Techniques
1. **Combining Traditional and Modern Methods**: Hybrid manufacturing techniques that combine traditional methods with modern technologies are gaining traction. For example, using 3D printing for prototyping followed by traditional methods for mass production can optimize both design flexibility and efficiency.
2. **Benefits of Hybrid Approaches in Terms of Cost and Quality**: Hybrid approaches can reduce costs by minimizing material waste and improving production efficiency while maintaining high-quality standards.
V. Quality Control and Testing
A. Importance of Quality Assurance in Capacitor Casing Manufacturing
Quality assurance is critical in capacitor casing manufacturing, as defects can lead to failures in electronic devices. Ensuring that casings meet stringent quality standards is essential for maintaining reliability and performance.
B. Latest Technologies in Quality Control
1. **Non-Destructive Testing Methods**: Advanced non-destructive testing (NDT) methods, such as ultrasonic testing and X-ray inspection, are being employed to detect defects without damaging the casings. These technologies provide real-time feedback and enhance quality assurance processes.
2. **Real-Time Monitoring Systems**: Implementing real-time monitoring systems allows manufacturers to track production processes and identify issues as they arise. This proactive approach helps maintain quality and reduces the likelihood of defects.
C. Regulatory Standards and Compliance
Manufacturers must adhere to various regulatory standards to ensure the safety and reliability of their products. Compliance with international standards, such as ISO and IEC, is essential for gaining market acceptance and ensuring product quality.
VI. Environmental Considerations
A. Sustainability in Capacitor Casing Manufacturing
1. **Reducing Carbon Footprint**: Manufacturers are increasingly focused on reducing their carbon footprint by optimizing production processes and utilizing sustainable materials. This shift not only benefits the environment but also enhances brand reputation.
2. **Recycling and Waste Management Practices**: Implementing effective recycling and waste management practices is crucial for minimizing environmental impact. Many manufacturers are exploring closed-loop systems that recycle materials used in production.
B. Innovations Aimed at Eco-Friendly Production
Innovations such as energy-efficient manufacturing processes and the use of renewable energy sources are becoming more common in capacitor casing production. These practices contribute to a more sustainable manufacturing ecosystem.
VII. Future Trends in Capacitor Casing Manufacturing
A. Predictions for the Next Decade
The capacitor casing manufacturing industry is poised for significant advancements in the coming decade. As technology continues to evolve, manufacturers will likely adopt more automated and sustainable practices.
B. Emerging Technologies and Their Potential Impact
Emerging technologies, such as artificial intelligence and machine learning, have the potential to revolutionize manufacturing processes. These technologies can optimize production schedules, improve quality control, and enhance design capabilities.
C. The Role of Industry 4.0 in Capacitor Manufacturing
Industry 4.0, characterized by the integration of digital technologies into manufacturing, will play a crucial role in the future of capacitor casing production. Smart factories equipped with IoT devices and data analytics will enable manufacturers to streamline operations and enhance efficiency.
VIII. Conclusion
In conclusion, the manufacturing processes for capacitor casings are evolving rapidly, driven by advancements in materials, technology, and sustainability practices. From traditional methods to innovative approaches like 3D printing and automation, manufacturers are finding new ways to enhance performance and reduce environmental impact. Staying updated with these advancements is essential for industry stakeholders to remain competitive and meet the growing demands of the electronic device market. As we look to the future, the integration of emerging technologies and a focus on sustainability will shape the next generation of capacitor casing manufacturing processes.
IX. References
A comprehensive list of academic papers, industry reports, and other resources used in the article would be included here to provide readers with further reading and validation of the information presented.
What are the Latest Manufacturing Processes for Capacitor Casings?
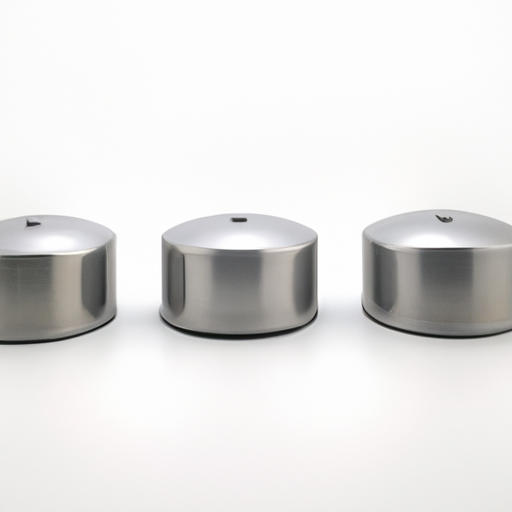
I. Introduction
Capacitors are essential components in electronic devices, serving as energy storage units that help regulate voltage and power flow. Their reliability and performance are critical to the overall functionality of electronic systems, from smartphones to industrial machinery. One of the key factors influencing a capacitor's performance is its casing, which protects the internal components and ensures durability under various operating conditions. This article explores the latest manufacturing processes for capacitor casings, highlighting innovations that enhance performance, sustainability, and efficiency.
II. Types of Capacitor Casings
Capacitor casings are made from various materials, each offering unique properties that affect the capacitor's performance.
A. Overview of Common Materials Used for Capacitor Casings
1. **Aluminum**: Aluminum casings are widely used due to their lightweight, corrosion resistance, and excellent thermal conductivity. They are particularly common in electrolytic capacitors.
2. **Plastic**: Plastic casings are favored for their versatility and cost-effectiveness. They can be molded into complex shapes, making them suitable for various capacitor designs.
3. **Ceramic**: Ceramic casings are known for their high dielectric strength and stability, making them ideal for high-frequency applications. They are often used in capacitors that require high reliability.
4. **Metalized Films**: These casings are made by depositing a thin layer of metal onto a dielectric film. They are lightweight and can be produced in various shapes, making them suitable for applications where space is limited.
B. Importance of Material Selection in Manufacturing Processes
The choice of material significantly impacts the manufacturing process, cost, and performance of the capacitor. For instance, aluminum casings may require stamping and forming techniques, while plastic casings can be produced using injection molding. Understanding the properties of each material helps manufacturers select the most appropriate processes for their specific applications.
III. Traditional Manufacturing Processes
A. Overview of Conventional Methods
1. **Stamping and Forming for Metal Casings**: Traditional methods for producing aluminum casings involve stamping sheets of metal into desired shapes. This process is efficient for high-volume production but can lead to material waste and limitations in design flexibility.
2. **Injection Molding for Plastic Casings**: Injection molding is a widely used technique for creating plastic casings. It allows for complex designs and high production rates but can be limited by the types of plastics that can be used and the initial setup costs.
B. Limitations of Traditional Processes
While traditional manufacturing methods have served the industry well, they come with several limitations:
1. **Material Waste**: Stamping processes often result in significant scrap material, leading to increased costs and environmental impact.
2. **Production Speed**: Although traditional methods can be efficient, they may not keep pace with the growing demand for rapid prototyping and customization.
3. **Design Flexibility**: Conventional methods can restrict design innovation, making it challenging to create unique or complex casing shapes.
IV. Latest Innovations in Manufacturing Processes
The capacitor casing manufacturing landscape is evolving, with several innovative processes emerging to address the limitations of traditional methods.
A. Advanced Materials
1. **Use of Nanomaterials for Enhanced Performance**: The incorporation of nanomaterials into capacitor casings can significantly enhance their performance. These materials can improve thermal conductivity, reduce weight, and increase the overall lifespan of capacitors.
2. **Biodegradable Materials for Environmentally Friendly Options**: As sustainability becomes a priority, manufacturers are exploring biodegradable materials for capacitor casings. These materials can reduce environmental impact and align with global efforts to minimize plastic waste.
B. Additive Manufacturing (3D Printing)
1. **Benefits of 3D Printing in Capacitor Casing Production**: Additive manufacturing, or 3D printing, allows for the creation of complex geometries that are difficult to achieve with traditional methods. This technology enables rapid prototyping, customization, and reduced material waste.
2. **Case Studies of Successful Implementations**: Companies like Panasonic and Vishay have successfully implemented 3D printing in their capacitor casing production, resulting in faster turnaround times and innovative designs that enhance performance.
C. Automation and Robotics
1. **Role of Automation in Improving Efficiency and Precision**: Automation technologies are revolutionizing capacitor casing manufacturing by increasing production speed and precision. Automated systems can handle repetitive tasks, reducing human error and improving overall quality.
2. **Examples of Robotic Applications in Casing Assembly**: Robotics are being used in various stages of the manufacturing process, from assembly to quality control. For instance, robotic arms can efficiently assemble capacitor components, ensuring consistent quality and reducing labor costs.
D. Hybrid Manufacturing Techniques
1. **Combining Traditional and Modern Methods**: Hybrid manufacturing techniques that combine traditional methods with modern technologies are gaining traction. For example, using 3D printing for prototyping followed by traditional methods for mass production can optimize both design flexibility and efficiency.
2. **Benefits of Hybrid Approaches in Terms of Cost and Quality**: Hybrid approaches can reduce costs by minimizing material waste and improving production efficiency while maintaining high-quality standards.
V. Quality Control and Testing
A. Importance of Quality Assurance in Capacitor Casing Manufacturing
Quality assurance is critical in capacitor casing manufacturing, as defects can lead to failures in electronic devices. Ensuring that casings meet stringent quality standards is essential for maintaining reliability and performance.
B. Latest Technologies in Quality Control
1. **Non-Destructive Testing Methods**: Advanced non-destructive testing (NDT) methods, such as ultrasonic testing and X-ray inspection, are being employed to detect defects without damaging the casings. These technologies provide real-time feedback and enhance quality assurance processes.
2. **Real-Time Monitoring Systems**: Implementing real-time monitoring systems allows manufacturers to track production processes and identify issues as they arise. This proactive approach helps maintain quality and reduces the likelihood of defects.
C. Regulatory Standards and Compliance
Manufacturers must adhere to various regulatory standards to ensure the safety and reliability of their products. Compliance with international standards, such as ISO and IEC, is essential for gaining market acceptance and ensuring product quality.
VI. Environmental Considerations
A. Sustainability in Capacitor Casing Manufacturing
1. **Reducing Carbon Footprint**: Manufacturers are increasingly focused on reducing their carbon footprint by optimizing production processes and utilizing sustainable materials. This shift not only benefits the environment but also enhances brand reputation.
2. **Recycling and Waste Management Practices**: Implementing effective recycling and waste management practices is crucial for minimizing environmental impact. Many manufacturers are exploring closed-loop systems that recycle materials used in production.
B. Innovations Aimed at Eco-Friendly Production
Innovations such as energy-efficient manufacturing processes and the use of renewable energy sources are becoming more common in capacitor casing production. These practices contribute to a more sustainable manufacturing ecosystem.
VII. Future Trends in Capacitor Casing Manufacturing
A. Predictions for the Next Decade
The capacitor casing manufacturing industry is poised for significant advancements in the coming decade. As technology continues to evolve, manufacturers will likely adopt more automated and sustainable practices.
B. Emerging Technologies and Their Potential Impact
Emerging technologies, such as artificial intelligence and machine learning, have the potential to revolutionize manufacturing processes. These technologies can optimize production schedules, improve quality control, and enhance design capabilities.
C. The Role of Industry 4.0 in Capacitor Manufacturing
Industry 4.0, characterized by the integration of digital technologies into manufacturing, will play a crucial role in the future of capacitor casing production. Smart factories equipped with IoT devices and data analytics will enable manufacturers to streamline operations and enhance efficiency.
VIII. Conclusion
In conclusion, the manufacturing processes for capacitor casings are evolving rapidly, driven by advancements in materials, technology, and sustainability practices. From traditional methods to innovative approaches like 3D printing and automation, manufacturers are finding new ways to enhance performance and reduce environmental impact. Staying updated with these advancements is essential for industry stakeholders to remain competitive and meet the growing demands of the electronic device market. As we look to the future, the integration of emerging technologies and a focus on sustainability will shape the next generation of capacitor casing manufacturing processes.
IX. References
A comprehensive list of academic papers, industry reports, and other resources used in the article would be included here to provide readers with further reading and validation of the information presented.