Latest Inductor Production Models for Equipment Components
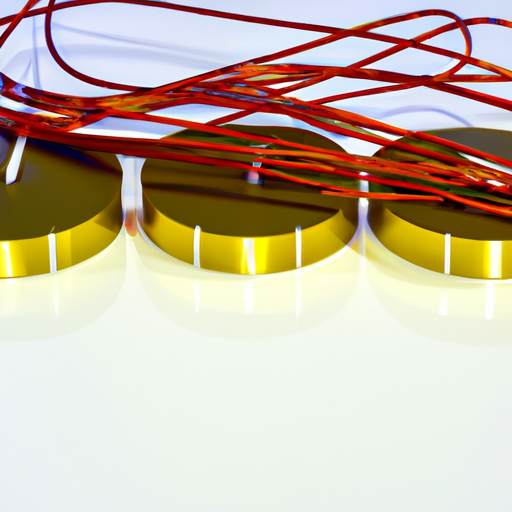
I. Introduction
Inductors are fundamental components in electronic circuits, serving as energy storage devices that store energy in a magnetic field when electrical current flows through them. They play a crucial role in various applications, including power supplies, filters, and oscillators. As technology advances, the demand for more efficient, compact, and high-performance inductors has led to the development of innovative production models. This article explores the latest trends and techniques in inductor production, highlighting their significance in modern technology.
II. Historical Context of Inductor Production
The technology behind inductors has evolved significantly over the years. Initially, inductors were produced using simple winding techniques with limited materials, which constrained their performance and application. Traditional production methods often resulted in larger, less efficient components that could not meet the growing demands of modern electronics.
As the electronics industry expanded, so did the need for more sophisticated inductor designs. The transition to modern production techniques has allowed manufacturers to create inductors that are not only smaller and more efficient but also capable of operating at higher frequencies. This evolution has paved the way for the latest production models that leverage advanced technologies and materials.
III. Current Trends in Inductor Production Models
A. Automation and Industry 4.0
The integration of automation and Industry 4.0 principles has revolutionized inductor manufacturing. Robotics play a significant role in streamlining production processes, reducing human error, and increasing efficiency. Automated systems can perform repetitive tasks with precision, allowing for higher output rates and consistent quality.
Moreover, the Internet of Things (IoT) has enabled real-time monitoring of production lines. Sensors embedded in manufacturing equipment can collect data on various parameters, such as temperature, humidity, and machine performance. This data can be analyzed to optimize production processes, predict maintenance needs, and ensure that inductors meet stringent quality standards.
B. Advanced Materials
The choice of materials is critical in inductor production, as it directly impacts performance. Recent advancements have seen the increased use of ferrite and composite materials, which offer improved magnetic properties and thermal stability. These materials allow for the design of inductors that can operate efficiently at higher frequencies and temperatures.
Nanotechnology is also making waves in inductor production. By manipulating materials at the nanoscale, manufacturers can enhance the magnetic properties of inductors, leading to better performance in compact designs. This trend towards advanced materials is essential for meeting the demands of modern electronic devices, which require smaller and more efficient components.
C. Miniaturization and High-Frequency Applications
As electronic devices become more compact, the trend towards miniaturization in inductor design has gained momentum. Smaller inductors are essential for fitting into tight spaces within devices while maintaining performance. However, this miniaturization presents challenges, particularly in high-frequency applications where inductors must maintain their efficiency and effectiveness.
Designing inductors for high-frequency applications requires careful consideration of factors such as parasitic capacitance and inductance. Manufacturers are increasingly focusing on innovative designs that minimize these effects, ensuring that inductors can perform optimally in demanding environments.
IV. Innovative Production Techniques
A. Additive Manufacturing (3D Printing)
Additive manufacturing, commonly known as 3D printing, is transforming the way inductors are produced. This technique allows for the creation of complex geometries that would be difficult or impossible to achieve with traditional methods. The benefits of 3D printing in inductor production include reduced material waste, shorter lead times, and the ability to customize designs for specific applications.
Several case studies have demonstrated the successful implementation of 3D printing in inductor production. For instance, manufacturers have used 3D printing to create inductors with intricate winding patterns that enhance performance while minimizing size. This innovative approach is paving the way for a new era of inductor design and production.
B. Automated Winding Technologies
Automated winding technologies have also emerged as a key innovation in inductor production. These processes utilize advanced machinery to wind wire around a core with high precision and speed. The advantages of automated winding include improved consistency, reduced labor costs, and enhanced production efficiency.
By automating the winding process, manufacturers can produce inductors with tighter tolerances and better performance characteristics. This technology is particularly beneficial for high-volume production, where maintaining quality and efficiency is paramount.
C. Hybrid Manufacturing Approaches
Hybrid manufacturing approaches combine traditional and modern techniques to optimize inductor production. By integrating established methods with innovative technologies, manufacturers can leverage the strengths of both approaches. For example, a hybrid model might involve using automated winding for precision while employing traditional assembly techniques for final product integration.
This combination allows for greater flexibility in production, enabling manufacturers to adapt to changing market demands and customer requirements. Hybrid models are becoming increasingly popular as they offer a balanced approach to efficiency and quality.
V. Quality Control and Testing in Inductor Production
A. Importance of Quality Assurance
Quality assurance is critical in inductor manufacturing, as even minor defects can lead to significant performance issues in electronic devices. Ensuring that inductors meet stringent quality standards is essential for maintaining reliability and customer satisfaction.
B. Latest Testing Methodologies
Recent advancements in testing methodologies have improved the ability to assess inductor performance. Electrical testing techniques, such as impedance and inductance measurements, are commonly used to evaluate the electrical characteristics of inductors. Additionally, environmental and stress testing helps ensure that inductors can withstand various operating conditions.
C. Role of AI and Machine Learning
Artificial intelligence (AI) and machine learning are increasingly being integrated into quality control processes. These technologies can analyze large datasets to identify patterns and anomalies, enabling manufacturers to detect potential issues before they escalate. By leveraging AI, manufacturers can enhance their quality assurance processes, leading to improved product reliability and performance.
VI. Environmental Considerations
A. Sustainable Practices
As the electronics industry faces growing scrutiny regarding its environmental impact, sustainable practices in inductor production have become a priority. Manufacturers are exploring ways to reduce energy consumption, minimize waste, and use eco-friendly materials in their production processes.
B. Recycling and Material Recovery
Recycling and material recovery processes are also gaining traction in the inductor manufacturing sector. By reclaiming materials from discarded inductors, manufacturers can reduce their reliance on virgin materials and contribute to a circular economy. This approach not only benefits the environment but also helps companies reduce costs.
C. Regulatory Compliance
Regulatory compliance is essential for manufacturers to ensure that their production processes meet environmental standards. Conducting thorough environmental impact assessments allows companies to identify potential risks and implement measures to mitigate them. Staying compliant with regulations is crucial for maintaining a positive reputation and avoiding legal issues.
VII. Future Directions in Inductor Production
A. Predictions for Technological Advancements
Looking ahead, the future of inductor production is likely to be shaped by continued technological advancements. Innovations in materials science, manufacturing techniques, and automation will drive the development of more efficient and high-performance inductors.
B. Potential Challenges
Despite the promising outlook, several challenges may hinder progress in inductor production. These include the need for skilled labor to operate advanced manufacturing technologies, the rising costs of raw materials, and the pressure to meet increasingly stringent environmental regulations.
C. Role of Research and Development
Research and development will play a crucial role in overcoming these challenges and shaping the future of inductor production. By investing in R&D, manufacturers can explore new materials, refine production techniques, and develop innovative designs that meet the evolving needs of the electronics industry.
VIII. Conclusion
In summary, the landscape of inductor production is rapidly evolving, driven by advancements in technology, materials, and manufacturing techniques. The integration of automation, IoT, and innovative production methods is enabling manufacturers to produce high-quality inductors that meet the demands of modern electronic devices. As the industry continues to evolve, staying updated with the latest production models will be essential for manufacturers to remain competitive and meet customer expectations. The future of inductor production holds great promise, with ongoing research and development paving the way for even more innovative solutions in the electronics industry.
IX. References
A comprehensive list of academic papers, industry reports, and other resources used in the article would be included here to provide readers with further reading and validation of the information presented.
Latest Inductor Production Models for Equipment Components
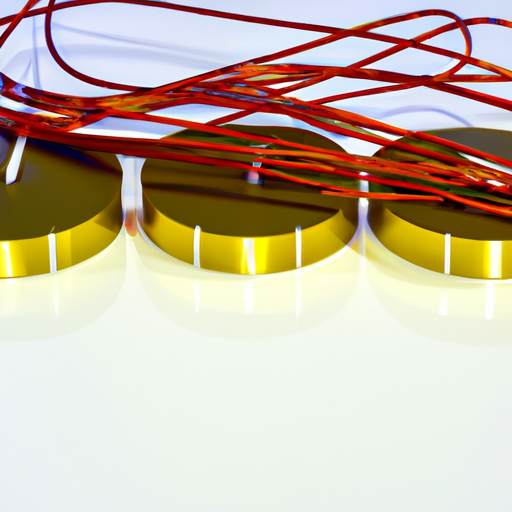
I. Introduction
Inductors are fundamental components in electronic circuits, serving as energy storage devices that store energy in a magnetic field when electrical current flows through them. They play a crucial role in various applications, including power supplies, filters, and oscillators. As technology advances, the demand for more efficient, compact, and high-performance inductors has led to the development of innovative production models. This article explores the latest trends and techniques in inductor production, highlighting their significance in modern technology.
II. Historical Context of Inductor Production
The technology behind inductors has evolved significantly over the years. Initially, inductors were produced using simple winding techniques with limited materials, which constrained their performance and application. Traditional production methods often resulted in larger, less efficient components that could not meet the growing demands of modern electronics.
As the electronics industry expanded, so did the need for more sophisticated inductor designs. The transition to modern production techniques has allowed manufacturers to create inductors that are not only smaller and more efficient but also capable of operating at higher frequencies. This evolution has paved the way for the latest production models that leverage advanced technologies and materials.
III. Current Trends in Inductor Production Models
A. Automation and Industry 4.0
The integration of automation and Industry 4.0 principles has revolutionized inductor manufacturing. Robotics play a significant role in streamlining production processes, reducing human error, and increasing efficiency. Automated systems can perform repetitive tasks with precision, allowing for higher output rates and consistent quality.
Moreover, the Internet of Things (IoT) has enabled real-time monitoring of production lines. Sensors embedded in manufacturing equipment can collect data on various parameters, such as temperature, humidity, and machine performance. This data can be analyzed to optimize production processes, predict maintenance needs, and ensure that inductors meet stringent quality standards.
B. Advanced Materials
The choice of materials is critical in inductor production, as it directly impacts performance. Recent advancements have seen the increased use of ferrite and composite materials, which offer improved magnetic properties and thermal stability. These materials allow for the design of inductors that can operate efficiently at higher frequencies and temperatures.
Nanotechnology is also making waves in inductor production. By manipulating materials at the nanoscale, manufacturers can enhance the magnetic properties of inductors, leading to better performance in compact designs. This trend towards advanced materials is essential for meeting the demands of modern electronic devices, which require smaller and more efficient components.
C. Miniaturization and High-Frequency Applications
As electronic devices become more compact, the trend towards miniaturization in inductor design has gained momentum. Smaller inductors are essential for fitting into tight spaces within devices while maintaining performance. However, this miniaturization presents challenges, particularly in high-frequency applications where inductors must maintain their efficiency and effectiveness.
Designing inductors for high-frequency applications requires careful consideration of factors such as parasitic capacitance and inductance. Manufacturers are increasingly focusing on innovative designs that minimize these effects, ensuring that inductors can perform optimally in demanding environments.
IV. Innovative Production Techniques
A. Additive Manufacturing (3D Printing)
Additive manufacturing, commonly known as 3D printing, is transforming the way inductors are produced. This technique allows for the creation of complex geometries that would be difficult or impossible to achieve with traditional methods. The benefits of 3D printing in inductor production include reduced material waste, shorter lead times, and the ability to customize designs for specific applications.
Several case studies have demonstrated the successful implementation of 3D printing in inductor production. For instance, manufacturers have used 3D printing to create inductors with intricate winding patterns that enhance performance while minimizing size. This innovative approach is paving the way for a new era of inductor design and production.
B. Automated Winding Technologies
Automated winding technologies have also emerged as a key innovation in inductor production. These processes utilize advanced machinery to wind wire around a core with high precision and speed. The advantages of automated winding include improved consistency, reduced labor costs, and enhanced production efficiency.
By automating the winding process, manufacturers can produce inductors with tighter tolerances and better performance characteristics. This technology is particularly beneficial for high-volume production, where maintaining quality and efficiency is paramount.
C. Hybrid Manufacturing Approaches
Hybrid manufacturing approaches combine traditional and modern techniques to optimize inductor production. By integrating established methods with innovative technologies, manufacturers can leverage the strengths of both approaches. For example, a hybrid model might involve using automated winding for precision while employing traditional assembly techniques for final product integration.
This combination allows for greater flexibility in production, enabling manufacturers to adapt to changing market demands and customer requirements. Hybrid models are becoming increasingly popular as they offer a balanced approach to efficiency and quality.
V. Quality Control and Testing in Inductor Production
A. Importance of Quality Assurance
Quality assurance is critical in inductor manufacturing, as even minor defects can lead to significant performance issues in electronic devices. Ensuring that inductors meet stringent quality standards is essential for maintaining reliability and customer satisfaction.
B. Latest Testing Methodologies
Recent advancements in testing methodologies have improved the ability to assess inductor performance. Electrical testing techniques, such as impedance and inductance measurements, are commonly used to evaluate the electrical characteristics of inductors. Additionally, environmental and stress testing helps ensure that inductors can withstand various operating conditions.
C. Role of AI and Machine Learning
Artificial intelligence (AI) and machine learning are increasingly being integrated into quality control processes. These technologies can analyze large datasets to identify patterns and anomalies, enabling manufacturers to detect potential issues before they escalate. By leveraging AI, manufacturers can enhance their quality assurance processes, leading to improved product reliability and performance.
VI. Environmental Considerations
A. Sustainable Practices
As the electronics industry faces growing scrutiny regarding its environmental impact, sustainable practices in inductor production have become a priority. Manufacturers are exploring ways to reduce energy consumption, minimize waste, and use eco-friendly materials in their production processes.
B. Recycling and Material Recovery
Recycling and material recovery processes are also gaining traction in the inductor manufacturing sector. By reclaiming materials from discarded inductors, manufacturers can reduce their reliance on virgin materials and contribute to a circular economy. This approach not only benefits the environment but also helps companies reduce costs.
C. Regulatory Compliance
Regulatory compliance is essential for manufacturers to ensure that their production processes meet environmental standards. Conducting thorough environmental impact assessments allows companies to identify potential risks and implement measures to mitigate them. Staying compliant with regulations is crucial for maintaining a positive reputation and avoiding legal issues.
VII. Future Directions in Inductor Production
A. Predictions for Technological Advancements
Looking ahead, the future of inductor production is likely to be shaped by continued technological advancements. Innovations in materials science, manufacturing techniques, and automation will drive the development of more efficient and high-performance inductors.
B. Potential Challenges
Despite the promising outlook, several challenges may hinder progress in inductor production. These include the need for skilled labor to operate advanced manufacturing technologies, the rising costs of raw materials, and the pressure to meet increasingly stringent environmental regulations.
C. Role of Research and Development
Research and development will play a crucial role in overcoming these challenges and shaping the future of inductor production. By investing in R&D, manufacturers can explore new materials, refine production techniques, and develop innovative designs that meet the evolving needs of the electronics industry.
VIII. Conclusion
In summary, the landscape of inductor production is rapidly evolving, driven by advancements in technology, materials, and manufacturing techniques. The integration of automation, IoT, and innovative production methods is enabling manufacturers to produce high-quality inductors that meet the demands of modern electronic devices. As the industry continues to evolve, staying updated with the latest production models will be essential for manufacturers to remain competitive and meet customer expectations. The future of inductor production holds great promise, with ongoing research and development paving the way for even more innovative solutions in the electronics industry.
IX. References
A comprehensive list of academic papers, industry reports, and other resources used in the article would be included here to provide readers with further reading and validation of the information presented.