Common Production Processes for Inductor Models
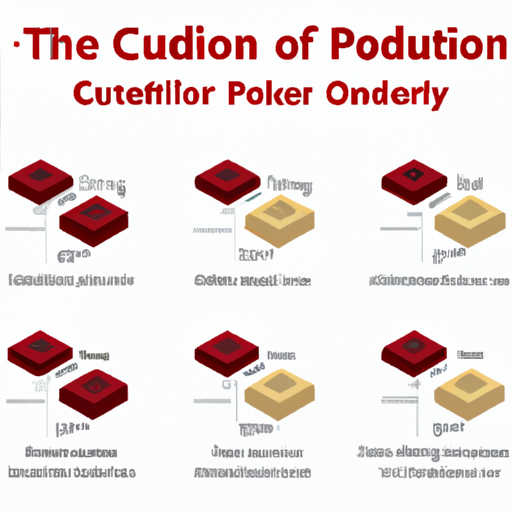
I. Introduction
Inductors are passive electronic components that store energy in a magnetic field when electrical current flows through them. They play a crucial role in various electronic circuits, including power supplies, filters, and oscillators. As the demand for more efficient and compact electronic devices grows, understanding the production processes for inductor models becomes increasingly important. This blog post will explore the common production processes for inductors, from raw materials to manufacturing techniques, quality control, and future trends.
II. Types of Inductors
Inductors come in various types, each designed for specific applications. The most common types include:
A. Air-core Inductors
Air-core inductors do not use a magnetic core, relying solely on the magnetic field generated by the wire winding. They are typically used in high-frequency applications due to their low losses and high Q-factor.
B. Iron-core Inductors
Iron-core inductors utilize an iron core to enhance inductance. The core material increases the magnetic field strength, making these inductors suitable for low-frequency applications, such as power supplies.
C. Ferrite-core Inductors
Ferrite-core inductors use ferrite materials, which are ceramic compounds that exhibit magnetic properties. These inductors are commonly used in high-frequency applications due to their low core losses and high permeability.
D. Other Specialized Inductors
Specialized inductors, such as toroidal and multilayer inductors, are designed for specific applications. Toroidal inductors have a doughnut-shaped core, which minimizes electromagnetic interference, while multilayer inductors are compact and suitable for surface-mount technology.
III. Raw Materials Used in Inductor Production
The production of inductors involves various raw materials, each contributing to the inductor's performance and characteristics.
A. Conductive Materials
Copper and aluminum are the most common conductive materials used for winding inductors. Copper is preferred for its excellent conductivity, while aluminum is lighter and more cost-effective.
B. Magnetic Materials
Ferrite and iron are the primary magnetic materials used in inductor cores. Ferrite is favored for high-frequency applications, while iron is used for low-frequency inductors due to its higher saturation flux density.
C. Insulating Materials
Insulating materials, such as polymers and ceramics, are essential for preventing short circuits between windings. These materials must withstand high temperatures and provide adequate dielectric strength.
D. Coatings and Finishes
Coatings and finishes protect inductors from environmental factors and enhance their performance. Common coatings include epoxy and polyurethane, which provide moisture resistance and mechanical protection.
IV. Design and Prototyping
The design and prototyping phase is critical in developing efficient and effective inductors.
A. Initial Design Considerations
Designing an inductor involves several considerations:
1. **Inductance Value**: The desired inductance value is determined based on the application requirements.
2. **Size and Form Factor**: The physical dimensions of the inductor must fit within the constraints of the electronic device.
3. **Frequency Response**: The inductor's performance at different frequencies is crucial for its intended application.
B. Prototyping Methods
Prototyping allows engineers to test and refine their designs before full-scale production. Common methods include:
1. **Computer-Aided Design (CAD)**: CAD software enables precise modeling of inductors, allowing for easy adjustments and simulations.
2. **Simulation Tools**: Simulation tools help predict the inductor's performance under various conditions, reducing the risk of design flaws.
3. **Rapid Prototyping Techniques**: Techniques such as 3D printing can create physical prototypes quickly, facilitating faster design iterations.
V. Manufacturing Processes
The manufacturing process for inductors involves several key steps:
A. Wire Winding
Wire winding is the first step in creating an inductor. This process can be done manually or through automated machines. Different winding techniques, such as single-layer and multi-layer winding, affect the inductor's performance and size.
B. Core Assembly
Once the wire is wound, the core assembly process begins. This involves selecting the appropriate core material, preparing it, and inserting it into the wound wire. Proper alignment is crucial to ensure optimal performance.
C. Insulation Application
Insulation is applied to prevent electrical shorts between the windings. Various insulation materials can be used, and application methods include dipping, spraying, and wrapping. The choice of insulation affects the inductor's thermal performance and reliability.
D. Soldering and Termination
The final step in the manufacturing process is soldering and termination. Different soldering techniques, such as wave and reflow soldering, are used to attach terminals to the inductor. The choice of terminal types and configurations depends on the intended application.
VI. Quality Control and Testing
Quality control is essential in inductor production to ensure reliability and performance.
A. Importance of Quality Control
Quality control processes help identify defects and ensure that inductors meet industry standards. This is crucial for maintaining customer trust and satisfaction.
B. Testing Methods
Several testing methods are employed to evaluate inductor performance:
1. **Inductance Measurement**: This test measures the inductance value to ensure it meets design specifications.
2. **DC Resistance Testing**: This test assesses the resistance of the winding, which affects efficiency.
3. **High-Frequency Performance Testing**: This test evaluates the inductor's performance at various frequencies, ensuring it meets application requirements.
C. Compliance with Industry Standards
Inductors must comply with industry standards, such as ISO and RoHS, to ensure safety and environmental responsibility.
VII. Packaging and Distribution
Once inductors pass quality control, they are packaged and prepared for distribution.
A. Packaging Materials and Methods
Packaging materials must protect inductors from physical damage and environmental factors. Common materials include anti-static bags and rigid boxes.
B. Labeling and Documentation
Proper labeling and documentation are essential for tracking and identifying inductors during distribution. This includes specifications, compliance certifications, and handling instructions.
C. Distribution Channels and Logistics
Inductor manufacturers must establish efficient distribution channels to deliver products to customers. This involves logistics planning, inventory management, and shipping arrangements.
VIII. Challenges in Inductor Production
The production of inductors faces several challenges:
A. Material Sourcing and Cost Fluctuations
The availability and cost of raw materials can fluctuate, impacting production costs and timelines. Manufacturers must develop strategies to mitigate these risks.
B. Technological Advancements
Rapid technological advancements require manufacturers to adapt their processes and designs continually. Staying competitive in the market necessitates ongoing investment in research and development.
C. Environmental Considerations and Sustainability
As environmental concerns grow, manufacturers must consider sustainable practices in their production processes. This includes reducing waste, recycling materials, and minimizing energy consumption.
IX. Future Trends in Inductor Production
The future of inductor production is shaped by several trends:
A. Innovations in Materials and Design
New materials and design techniques are emerging, allowing for more efficient and compact inductors. Innovations such as nanomaterials and advanced core designs are being explored.
B. Automation and Industry 4.0
The integration of automation and Industry 4.0 technologies is transforming inductor manufacturing. Smart factories equipped with IoT devices and AI can optimize production processes and improve efficiency.
C. The Role of Inductors in Emerging Technologies
Inductors are becoming increasingly important in emerging technologies, such as electric vehicles and renewable energy systems. As these industries grow, the demand for high-performance inductors will continue to rise.
X. Conclusion
Inductors are vital components in electronic circuits, and understanding their production processes is essential for manufacturers and engineers alike. From raw materials to manufacturing techniques, quality control, and future trends, the production of inductors is a complex and evolving field. As technology advances and the demand for efficient electronic devices grows, the inductor manufacturing industry will continue to adapt and innovate, ensuring that these essential components meet the needs of the future.
Common Production Processes for Inductor Models
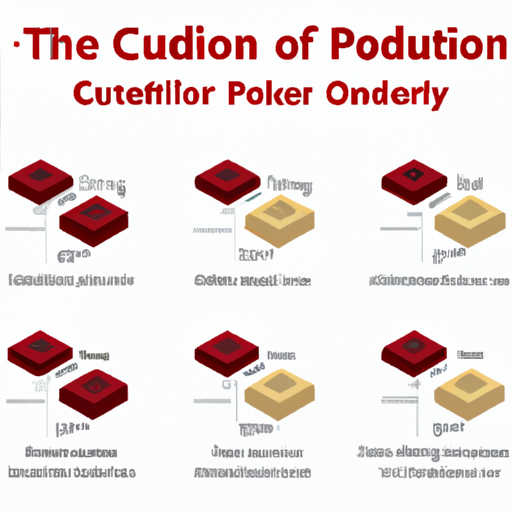
I. Introduction
Inductors are passive electronic components that store energy in a magnetic field when electrical current flows through them. They play a crucial role in various electronic circuits, including power supplies, filters, and oscillators. As the demand for more efficient and compact electronic devices grows, understanding the production processes for inductor models becomes increasingly important. This blog post will explore the common production processes for inductors, from raw materials to manufacturing techniques, quality control, and future trends.
II. Types of Inductors
Inductors come in various types, each designed for specific applications. The most common types include:
A. Air-core Inductors
Air-core inductors do not use a magnetic core, relying solely on the magnetic field generated by the wire winding. They are typically used in high-frequency applications due to their low losses and high Q-factor.
B. Iron-core Inductors
Iron-core inductors utilize an iron core to enhance inductance. The core material increases the magnetic field strength, making these inductors suitable for low-frequency applications, such as power supplies.
C. Ferrite-core Inductors
Ferrite-core inductors use ferrite materials, which are ceramic compounds that exhibit magnetic properties. These inductors are commonly used in high-frequency applications due to their low core losses and high permeability.
D. Other Specialized Inductors
Specialized inductors, such as toroidal and multilayer inductors, are designed for specific applications. Toroidal inductors have a doughnut-shaped core, which minimizes electromagnetic interference, while multilayer inductors are compact and suitable for surface-mount technology.
III. Raw Materials Used in Inductor Production
The production of inductors involves various raw materials, each contributing to the inductor's performance and characteristics.
A. Conductive Materials
Copper and aluminum are the most common conductive materials used for winding inductors. Copper is preferred for its excellent conductivity, while aluminum is lighter and more cost-effective.
B. Magnetic Materials
Ferrite and iron are the primary magnetic materials used in inductor cores. Ferrite is favored for high-frequency applications, while iron is used for low-frequency inductors due to its higher saturation flux density.
C. Insulating Materials
Insulating materials, such as polymers and ceramics, are essential for preventing short circuits between windings. These materials must withstand high temperatures and provide adequate dielectric strength.
D. Coatings and Finishes
Coatings and finishes protect inductors from environmental factors and enhance their performance. Common coatings include epoxy and polyurethane, which provide moisture resistance and mechanical protection.
IV. Design and Prototyping
The design and prototyping phase is critical in developing efficient and effective inductors.
A. Initial Design Considerations
Designing an inductor involves several considerations:
1. **Inductance Value**: The desired inductance value is determined based on the application requirements.
2. **Size and Form Factor**: The physical dimensions of the inductor must fit within the constraints of the electronic device.
3. **Frequency Response**: The inductor's performance at different frequencies is crucial for its intended application.
B. Prototyping Methods
Prototyping allows engineers to test and refine their designs before full-scale production. Common methods include:
1. **Computer-Aided Design (CAD)**: CAD software enables precise modeling of inductors, allowing for easy adjustments and simulations.
2. **Simulation Tools**: Simulation tools help predict the inductor's performance under various conditions, reducing the risk of design flaws.
3. **Rapid Prototyping Techniques**: Techniques such as 3D printing can create physical prototypes quickly, facilitating faster design iterations.
V. Manufacturing Processes
The manufacturing process for inductors involves several key steps:
A. Wire Winding
Wire winding is the first step in creating an inductor. This process can be done manually or through automated machines. Different winding techniques, such as single-layer and multi-layer winding, affect the inductor's performance and size.
B. Core Assembly
Once the wire is wound, the core assembly process begins. This involves selecting the appropriate core material, preparing it, and inserting it into the wound wire. Proper alignment is crucial to ensure optimal performance.
C. Insulation Application
Insulation is applied to prevent electrical shorts between the windings. Various insulation materials can be used, and application methods include dipping, spraying, and wrapping. The choice of insulation affects the inductor's thermal performance and reliability.
D. Soldering and Termination
The final step in the manufacturing process is soldering and termination. Different soldering techniques, such as wave and reflow soldering, are used to attach terminals to the inductor. The choice of terminal types and configurations depends on the intended application.
VI. Quality Control and Testing
Quality control is essential in inductor production to ensure reliability and performance.
A. Importance of Quality Control
Quality control processes help identify defects and ensure that inductors meet industry standards. This is crucial for maintaining customer trust and satisfaction.
B. Testing Methods
Several testing methods are employed to evaluate inductor performance:
1. **Inductance Measurement**: This test measures the inductance value to ensure it meets design specifications.
2. **DC Resistance Testing**: This test assesses the resistance of the winding, which affects efficiency.
3. **High-Frequency Performance Testing**: This test evaluates the inductor's performance at various frequencies, ensuring it meets application requirements.
C. Compliance with Industry Standards
Inductors must comply with industry standards, such as ISO and RoHS, to ensure safety and environmental responsibility.
VII. Packaging and Distribution
Once inductors pass quality control, they are packaged and prepared for distribution.
A. Packaging Materials and Methods
Packaging materials must protect inductors from physical damage and environmental factors. Common materials include anti-static bags and rigid boxes.
B. Labeling and Documentation
Proper labeling and documentation are essential for tracking and identifying inductors during distribution. This includes specifications, compliance certifications, and handling instructions.
C. Distribution Channels and Logistics
Inductor manufacturers must establish efficient distribution channels to deliver products to customers. This involves logistics planning, inventory management, and shipping arrangements.
VIII. Challenges in Inductor Production
The production of inductors faces several challenges:
A. Material Sourcing and Cost Fluctuations
The availability and cost of raw materials can fluctuate, impacting production costs and timelines. Manufacturers must develop strategies to mitigate these risks.
B. Technological Advancements
Rapid technological advancements require manufacturers to adapt their processes and designs continually. Staying competitive in the market necessitates ongoing investment in research and development.
C. Environmental Considerations and Sustainability
As environmental concerns grow, manufacturers must consider sustainable practices in their production processes. This includes reducing waste, recycling materials, and minimizing energy consumption.
IX. Future Trends in Inductor Production
The future of inductor production is shaped by several trends:
A. Innovations in Materials and Design
New materials and design techniques are emerging, allowing for more efficient and compact inductors. Innovations such as nanomaterials and advanced core designs are being explored.
B. Automation and Industry 4.0
The integration of automation and Industry 4.0 technologies is transforming inductor manufacturing. Smart factories equipped with IoT devices and AI can optimize production processes and improve efficiency.
C. The Role of Inductors in Emerging Technologies
Inductors are becoming increasingly important in emerging technologies, such as electric vehicles and renewable energy systems. As these industries grow, the demand for high-performance inductors will continue to rise.
X. Conclusion
Inductors are vital components in electronic circuits, and understanding their production processes is essential for manufacturers and engineers alike. From raw materials to manufacturing techniques, quality control, and future trends, the production of inductors is a complex and evolving field. As technology advances and the demand for efficient electronic devices grows, the inductor manufacturing industry will continue to adapt and innovate, ensuring that these essential components meet the needs of the future.