The Production Process of Mainstream Capacitor Manufacturers
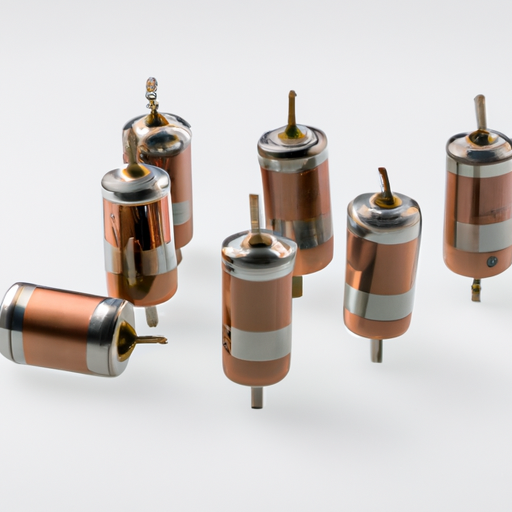
I. Introduction
Capacitors are essential components in electronic devices, serving as energy storage units that help regulate voltage and current. They play a critical role in various applications, from consumer electronics to industrial machinery. As the demand for electronic devices continues to rise, the capacitor manufacturing industry has evolved to meet the needs of modern technology. This blog post will explore the production process of mainstream capacitor manufacturers, detailing the types of capacitors, raw materials, manufacturing steps, and future trends in the industry.
II. Types of Capacitors
Capacitors come in various types, each designed for specific applications and performance characteristics. The most common types include:
A. Electrolytic Capacitors
Electrolytic capacitors are polarized components that offer high capacitance values in a compact size. They are widely used in power supply circuits and audio applications due to their ability to handle large voltage fluctuations.
B. Ceramic Capacitors
Ceramic capacitors are non-polarized and known for their stability and reliability. They are commonly used in high-frequency applications, such as RF circuits and decoupling applications.
C. Film Capacitors
Film capacitors utilize a thin plastic film as the dielectric material. They are known for their low loss and high insulation resistance, making them suitable for audio and power applications.
D. Tantalum Capacitors
Tantalum capacitors are known for their high capacitance-to-volume ratio and stability. They are often used in applications where space is limited, such as in mobile devices and medical equipment.
E. Other Specialized Capacitors
In addition to the above types, there are specialized capacitors designed for specific applications, such as supercapacitors for energy storage and ceramic capacitors for high-voltage applications.
III. Raw Materials Used in Capacitor Production
The production of capacitors requires a variety of raw materials, each contributing to the performance and reliability of the final product.
A. Dielectric Materials
The dielectric material is crucial for a capacitor's performance. Common dielectric materials include ceramic, polyester, and tantalum oxide. Manufacturers must ensure the quality and consistency of these materials through rigorous sourcing and quality control processes.
B. Conductive Materials
Conductive materials, such as aluminum and tantalum, are used for the electrodes in capacitors. The manufacturing process often involves coating and plating these metals to enhance conductivity and prevent corrosion.
C. Packaging Materials
The packaging of capacitors is vital for their performance and longevity. Manufacturers use various materials, including plastic and metal, to protect the internal components from environmental factors and mechanical stress.
IV. The Manufacturing Process
The manufacturing process of capacitors involves several key steps, each critical to ensuring the quality and performance of the final product.
A. Design and Engineering
The production process begins with design and engineering. Manufacturers consider factors such as capacitance, voltage rating, and size during the initial design phase. Advanced simulation tools are often used to prototype designs and predict performance.
B. Material Preparation
Once the design is finalized, manufacturers source and test raw materials. This step includes pre-processing materials to ensure they meet the required specifications for dielectric and conductive properties.
C. Component Fabrication
The fabrication of components involves several sub-steps:
1. **Dielectric Layer Formation**: The dielectric material is processed to create thin layers that will be used in the capacitor.
2. **Electrode Preparation**: Conductive materials are shaped and treated to form the electrodes.
3. **Assembly of Components**: The dielectric layers and electrodes are assembled to create the capacitor structure.
D. Encapsulation and Packaging
After assembly, capacitors undergo encapsulation to protect them from environmental factors. Various methods, such as resin coating and heat-shrink tubing, are employed. Quality assurance is critical during this stage to ensure that the packaging does not compromise the capacitor's performance.
E. Testing and Quality Control
The final step in the manufacturing process involves rigorous testing and quality control. Capacitors undergo electrical testing to verify capacitance and voltage ratings, environmental testing to assess performance under different conditions, and reliability testing to ensure long-term performance.
V. Automation and Technology in Capacitor Manufacturing
The capacitor manufacturing industry has embraced automation and advanced technologies to enhance production efficiency and product quality.
A. Role of Automation in Production Efficiency
Automation plays a significant role in streamlining the manufacturing process. Automated machinery can perform repetitive tasks with precision, reducing the risk of human error and increasing production speed.
B. Advanced Manufacturing Technologies
Emerging technologies, such as 3D printing and artificial intelligence, are beginning to influence capacitor manufacturing. These technologies allow for more complex designs and faster prototyping, enabling manufacturers to respond quickly to market demands.
C. Industry 4.0 and Smart Manufacturing
The concept of Industry 4.0, which integrates IoT and data analytics into manufacturing processes, is transforming the capacitor industry. Smart manufacturing systems can monitor production in real-time, optimizing processes and reducing waste.
VI. Environmental Considerations
As the capacitor manufacturing industry grows, so does the need for sustainable practices.
A. Sustainable Sourcing of Materials
Manufacturers are increasingly focused on sourcing materials sustainably, ensuring that their supply chains are environmentally responsible.
B. Waste Management and Recycling
Effective waste management practices are essential in minimizing the environmental impact of capacitor production. Many manufacturers are implementing recycling programs to reclaim materials from defective or obsolete capacitors.
C. Compliance with Environmental Regulations
Compliance with environmental regulations is crucial for capacitor manufacturers. Adhering to these regulations not only helps protect the environment but also enhances the company's reputation and marketability.
VII. Challenges in Capacitor Manufacturing
Despite advancements in technology and processes, the capacitor manufacturing industry faces several challenges.
A. Supply Chain Issues
Global supply chain disruptions can impact the availability of raw materials, leading to production delays and increased costs.
B. Technological Advancements and Competition
Rapid technological advancements require manufacturers to continuously innovate to stay competitive. This can be a significant challenge, especially for smaller companies with limited resources.
C. Market Demand Fluctuations
The demand for capacitors can fluctuate based on market trends and technological developments. Manufacturers must be agile and responsive to these changes to maintain profitability.
VIII. Future Trends in Capacitor Manufacturing
The capacitor manufacturing industry is poised for significant changes in the coming years.
A. Innovations in Capacitor Technology
Research and development efforts are focused on creating capacitors with higher energy densities, faster charge/discharge rates, and improved reliability.
B. Emerging Markets and Applications
As technology evolves, new markets and applications for capacitors are emerging, particularly in electric vehicles and renewable energy systems.
C. The Impact of Electric Vehicles and Renewable Energy
The rise of electric vehicles and renewable energy sources is driving demand for advanced capacitors, particularly in energy storage applications. Manufacturers are adapting their production processes to meet these new demands.
IX. Conclusion
The production process of mainstream capacitor manufacturers is a complex and multifaceted endeavor that involves careful consideration of materials, design, and technology. Capacitors play a vital role in modern electronics, and as the industry continues to evolve, manufacturers must adapt to new challenges and opportunities. The future of capacitor manufacturing looks promising, with innovations on the horizon that will enhance performance and sustainability.
X. References
- Academic journals on capacitor technology and manufacturing processes.
- Industry reports detailing market trends and forecasts.
- Case studies from leading capacitor manufacturers showcasing best practices and innovations.
This comprehensive overview of the capacitor production process highlights the importance of these components in modern technology and the ongoing advancements within the industry. As we move forward, the capacitor manufacturing sector will continue to play a crucial role in shaping the future of electronics.
The Production Process of Mainstream Capacitor Manufacturers
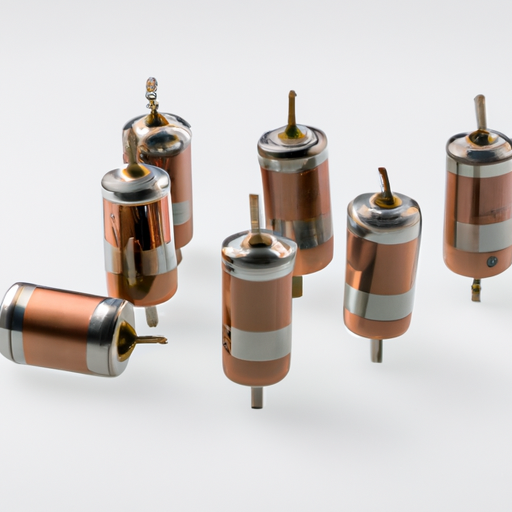
I. Introduction
Capacitors are essential components in electronic devices, serving as energy storage units that help regulate voltage and current. They play a critical role in various applications, from consumer electronics to industrial machinery. As the demand for electronic devices continues to rise, the capacitor manufacturing industry has evolved to meet the needs of modern technology. This blog post will explore the production process of mainstream capacitor manufacturers, detailing the types of capacitors, raw materials, manufacturing steps, and future trends in the industry.
II. Types of Capacitors
Capacitors come in various types, each designed for specific applications and performance characteristics. The most common types include:
A. Electrolytic Capacitors
Electrolytic capacitors are polarized components that offer high capacitance values in a compact size. They are widely used in power supply circuits and audio applications due to their ability to handle large voltage fluctuations.
B. Ceramic Capacitors
Ceramic capacitors are non-polarized and known for their stability and reliability. They are commonly used in high-frequency applications, such as RF circuits and decoupling applications.
C. Film Capacitors
Film capacitors utilize a thin plastic film as the dielectric material. They are known for their low loss and high insulation resistance, making them suitable for audio and power applications.
D. Tantalum Capacitors
Tantalum capacitors are known for their high capacitance-to-volume ratio and stability. They are often used in applications where space is limited, such as in mobile devices and medical equipment.
E. Other Specialized Capacitors
In addition to the above types, there are specialized capacitors designed for specific applications, such as supercapacitors for energy storage and ceramic capacitors for high-voltage applications.
III. Raw Materials Used in Capacitor Production
The production of capacitors requires a variety of raw materials, each contributing to the performance and reliability of the final product.
A. Dielectric Materials
The dielectric material is crucial for a capacitor's performance. Common dielectric materials include ceramic, polyester, and tantalum oxide. Manufacturers must ensure the quality and consistency of these materials through rigorous sourcing and quality control processes.
B. Conductive Materials
Conductive materials, such as aluminum and tantalum, are used for the electrodes in capacitors. The manufacturing process often involves coating and plating these metals to enhance conductivity and prevent corrosion.
C. Packaging Materials
The packaging of capacitors is vital for their performance and longevity. Manufacturers use various materials, including plastic and metal, to protect the internal components from environmental factors and mechanical stress.
IV. The Manufacturing Process
The manufacturing process of capacitors involves several key steps, each critical to ensuring the quality and performance of the final product.
A. Design and Engineering
The production process begins with design and engineering. Manufacturers consider factors such as capacitance, voltage rating, and size during the initial design phase. Advanced simulation tools are often used to prototype designs and predict performance.
B. Material Preparation
Once the design is finalized, manufacturers source and test raw materials. This step includes pre-processing materials to ensure they meet the required specifications for dielectric and conductive properties.
C. Component Fabrication
The fabrication of components involves several sub-steps:
1. **Dielectric Layer Formation**: The dielectric material is processed to create thin layers that will be used in the capacitor.
2. **Electrode Preparation**: Conductive materials are shaped and treated to form the electrodes.
3. **Assembly of Components**: The dielectric layers and electrodes are assembled to create the capacitor structure.
D. Encapsulation and Packaging
After assembly, capacitors undergo encapsulation to protect them from environmental factors. Various methods, such as resin coating and heat-shrink tubing, are employed. Quality assurance is critical during this stage to ensure that the packaging does not compromise the capacitor's performance.
E. Testing and Quality Control
The final step in the manufacturing process involves rigorous testing and quality control. Capacitors undergo electrical testing to verify capacitance and voltage ratings, environmental testing to assess performance under different conditions, and reliability testing to ensure long-term performance.
V. Automation and Technology in Capacitor Manufacturing
The capacitor manufacturing industry has embraced automation and advanced technologies to enhance production efficiency and product quality.
A. Role of Automation in Production Efficiency
Automation plays a significant role in streamlining the manufacturing process. Automated machinery can perform repetitive tasks with precision, reducing the risk of human error and increasing production speed.
B. Advanced Manufacturing Technologies
Emerging technologies, such as 3D printing and artificial intelligence, are beginning to influence capacitor manufacturing. These technologies allow for more complex designs and faster prototyping, enabling manufacturers to respond quickly to market demands.
C. Industry 4.0 and Smart Manufacturing
The concept of Industry 4.0, which integrates IoT and data analytics into manufacturing processes, is transforming the capacitor industry. Smart manufacturing systems can monitor production in real-time, optimizing processes and reducing waste.
VI. Environmental Considerations
As the capacitor manufacturing industry grows, so does the need for sustainable practices.
A. Sustainable Sourcing of Materials
Manufacturers are increasingly focused on sourcing materials sustainably, ensuring that their supply chains are environmentally responsible.
B. Waste Management and Recycling
Effective waste management practices are essential in minimizing the environmental impact of capacitor production. Many manufacturers are implementing recycling programs to reclaim materials from defective or obsolete capacitors.
C. Compliance with Environmental Regulations
Compliance with environmental regulations is crucial for capacitor manufacturers. Adhering to these regulations not only helps protect the environment but also enhances the company's reputation and marketability.
VII. Challenges in Capacitor Manufacturing
Despite advancements in technology and processes, the capacitor manufacturing industry faces several challenges.
A. Supply Chain Issues
Global supply chain disruptions can impact the availability of raw materials, leading to production delays and increased costs.
B. Technological Advancements and Competition
Rapid technological advancements require manufacturers to continuously innovate to stay competitive. This can be a significant challenge, especially for smaller companies with limited resources.
C. Market Demand Fluctuations
The demand for capacitors can fluctuate based on market trends and technological developments. Manufacturers must be agile and responsive to these changes to maintain profitability.
VIII. Future Trends in Capacitor Manufacturing
The capacitor manufacturing industry is poised for significant changes in the coming years.
A. Innovations in Capacitor Technology
Research and development efforts are focused on creating capacitors with higher energy densities, faster charge/discharge rates, and improved reliability.
B. Emerging Markets and Applications
As technology evolves, new markets and applications for capacitors are emerging, particularly in electric vehicles and renewable energy systems.
C. The Impact of Electric Vehicles and Renewable Energy
The rise of electric vehicles and renewable energy sources is driving demand for advanced capacitors, particularly in energy storage applications. Manufacturers are adapting their production processes to meet these new demands.
IX. Conclusion
The production process of mainstream capacitor manufacturers is a complex and multifaceted endeavor that involves careful consideration of materials, design, and technology. Capacitors play a vital role in modern electronics, and as the industry continues to evolve, manufacturers must adapt to new challenges and opportunities. The future of capacitor manufacturing looks promising, with innovations on the horizon that will enhance performance and sustainability.
X. References
- Academic journals on capacitor technology and manufacturing processes.
- Industry reports detailing market trends and forecasts.
- Case studies from leading capacitor manufacturers showcasing best practices and innovations.
This comprehensive overview of the capacitor production process highlights the importance of these components in modern technology and the ongoing advancements within the industry. As we move forward, the capacitor manufacturing sector will continue to play a crucial role in shaping the future of electronics.